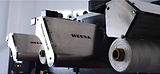
DTX- 300
The DTX-300 is a 2x1 twisting machine for the production of all types of technical yarns; it is unique in the market for price and performance, and displaces the ring twisters.
Flexibility is maximum as each position is independent and the precision winder at the top of the machine can also be used separately as assembly winder without twisting or rewinder.
A side creel can be added to the machine for the case of the upper winder is used separately as
assembly winder.




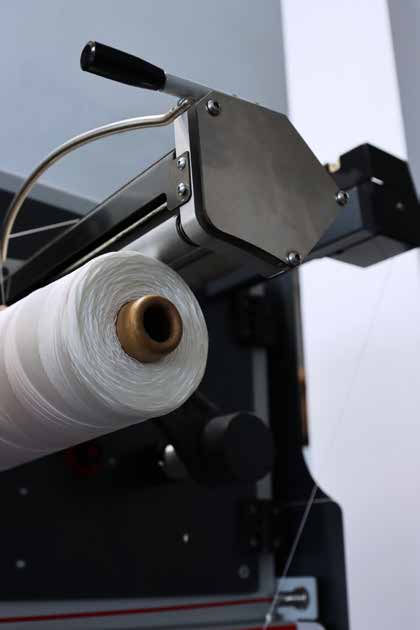
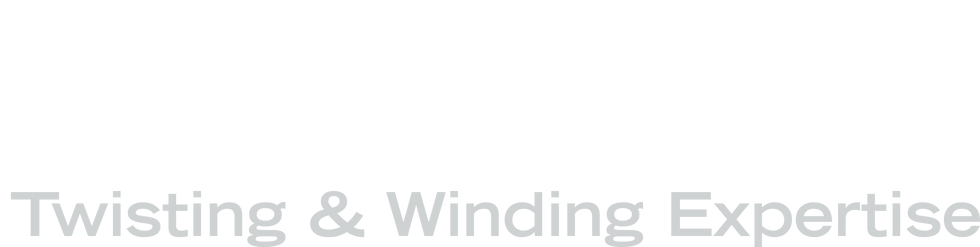
STANDARD EQUIPMENT
-
Program so winder can operate independently of part of the twister, being fet from the front creel.
-
PLC to modify all parameters and memorize them in more than 100 files.
-
Spindle motor, winding motor and capstan motor for the tension control; and there 3 inveters.
-
Yarn breaking detector by means exact tension control device which detects any missed thread.
-
2% of the value of the machine in spare parts and accessories.
OPERATION OF THE PRECISION WINDER ONLY
-
Front creel for 6 bobbins per position +6 in reserve, which can be up to 12 using the creel bobbins from the adjacent positions. Until 24 without reserve.
-
Yarn breaking detector able for 12 threads per each twisting position, instead of 6, so the reserve bobbin can function as the main bobbin.
-
Switch to use the creel broken thread detector from position 2 to position 1 when more than 12 plies.
OPTIONAL EQUIPMENT
WITH OPERATION OF THE TWISTING MACHINE AND PRECISION WINDER TOGETHER
-
Yarn coating Kiss Roll type thread impregnation system.
-
Stroboscope.
-
Flyer arm.
-
MAXIMUM TENACITY AT HIGH SPEEDS: Thread contact points with specific materials depending on the technical yarn to be twisted. Example: The control rings made of special materials (Brass, Matte hard chrome, Steel, Delrin).
-
PATENTED TPRX GADGET (2x1 SóZ inside 2x1 ZóS for 1st and 2nd twist and rewind in a single step. REMOVABLE PART).
-
Conical bobbin in the 3º30' winding or other measurements.
-
Parallel winding in K-200 spool or other sizes, for monofilaments.
SPINDLE SPEED
7000 rpm x 2 (double twist) = 14,000 rpm
WINDING SPEED WITH TWIST
up to 300 meters/minute
ASSEMBLY WINDING SPEED WITHOUT TWIST
up to 600 meters/minute
REWINDING SPEED WITHOUT TWIST
up to 400 meters/minute
TWIST PER MINUTE
14,000 tpm x 3 spindles = 42,000 tmp
FINAL BOBBIN, Usual Diameter
300 mm x 250 mm (10” traverse)
Tube or Without tube: According to preference;
Tailor made tube diameter with pneumatic or mechanical fixation.
Other traverses: 4”,6”,8”,12” (on request).
Net Weight
Polyethylene or Polypropylene: 10 Kg
Polyamide: 12 Kg
Polyester: 15 Kg
Aramid: 18 Kg
TECHNICALCHARACTERISTICS

XMINI TWISTER 300-300 DENIER
-
Monoblock machine. No assembly required.
-
Twisting and precision winding on cardboard tube in one step.
-
3-position Extendable Module: 42,000 Twists/Minute.
-
All parameters: Twist, Winding, Tension, Length, etc adjustable in PLC.
-
Usual final precision package of 250 x 300 mm to obtain up to 10-18Kg depending on the material.
-
Open Electronics: It does not depend on machinery manufacturer.
-
Continuous technical and after-sales support from CODINA.
-
Independent twisting and winding per position, and also the upper part can be used as a separate assembly or precision winder, feeding from outside
the machine. -
Double twist lower pot for single strand bobbins or for threads previously assembled in the upper winding or in a separated assembly winder, that we
also suply.
-
Examples of consumption:
0,25 kW/h/Kg con 1.000 Denier.
0,05 Kw/h/Kg con 25.000 Denier. -
Noise level less than 30 dB. Very quiet.
-
Pneumatic threading (very efficient).
-
Front creel to join X plies until reaching the desired Denier.
-
Possibility of obtaining the 1st twist in the upper precision winding of the 3 positions and then the 2nd twist in the upper precision winding of the
central position. (Putting together and twisting the 3 bobbins obtained previously placed in each pot).